天然氣發(fā)電機(jī)組曲軸的光磨加工情況,是保證修復(fù)質(zhì)量的關(guān)鍵工序之一。以正時(shí)齒輪軸頸和飛輪突緣的外圓表面作為光磨裝-膏基準(zhǔn)時(shí),必須先校正彎曲度再進(jìn)行磨削,磨前中間主軸頸的擺差不得大于o.3毫米。如果不預(yù)先校正彎曲,織削以后將會(huì)使曲軸產(chǎn)生與原來(lái)飛輪突緣和正時(shí)齒輪軸線交叉的新軸線,改變了回轉(zhuǎn)半徑,破壞了動(dòng)平衡力,縮短使用壽命,加劇有關(guān)零件的磨耗,正時(shí)齒輪的響聲也大,后油封漏汕,增加了發(fā)動(dòng)機(jī)的不平衡旋轉(zhuǎn)質(zhì)量。
The smooth grinding of the crankshaft of natural gas generator set is one of the key processes to ensure the repair quality. When the outer circle surface of the timing gear journal and the flywheel flange is used as the basis for smooth grinding, the curvature must be corrected before grinding, and the runout of the intermediate main journal before grinding shall not be greater than 0.3 mm. If the bending is not corrected in advance, after weaving, the crankshaft will produce a new axis that intersects with the original flywheel flange and the axis of the timing gear, which changes the turning radius, destroys the dynamic balance force, shortens the service life, and intensifies the wear of relevant parts. The noise of the timing gear is also loud, and the rear oil seal leaks, which increases the unbalanced rotating quality of the engine.
嚴(yán)格保證天然氣發(fā)電機(jī)組曲軸軸頸圓角半徑的尺寸符合圖紙要求,是修復(fù)質(zhì)量的關(guān)鍵性問(wèn)題之一。但一般汽車修理廠對(duì)此并沒(méi)有足夠的重視,砂輪很少修磨,光磨的圓角半徑常小于規(guī)定的尺寸。有資料統(tǒng)計(jì),圓角半徑小于2,5毫米,其疲勞強(qiáng)度只及圓角半徑為2.5毫米的80%以下。由于對(duì)光磨曲軸的砂輪,經(jīng)常用磨床附屬的砂輪圓角校正器修整,使磨得圓角尺寸符合要求,所以自振動(dòng)堆焊投產(chǎn)以來(lái),沒(méi)有發(fā)生過(guò)斷軸現(xiàn)象。
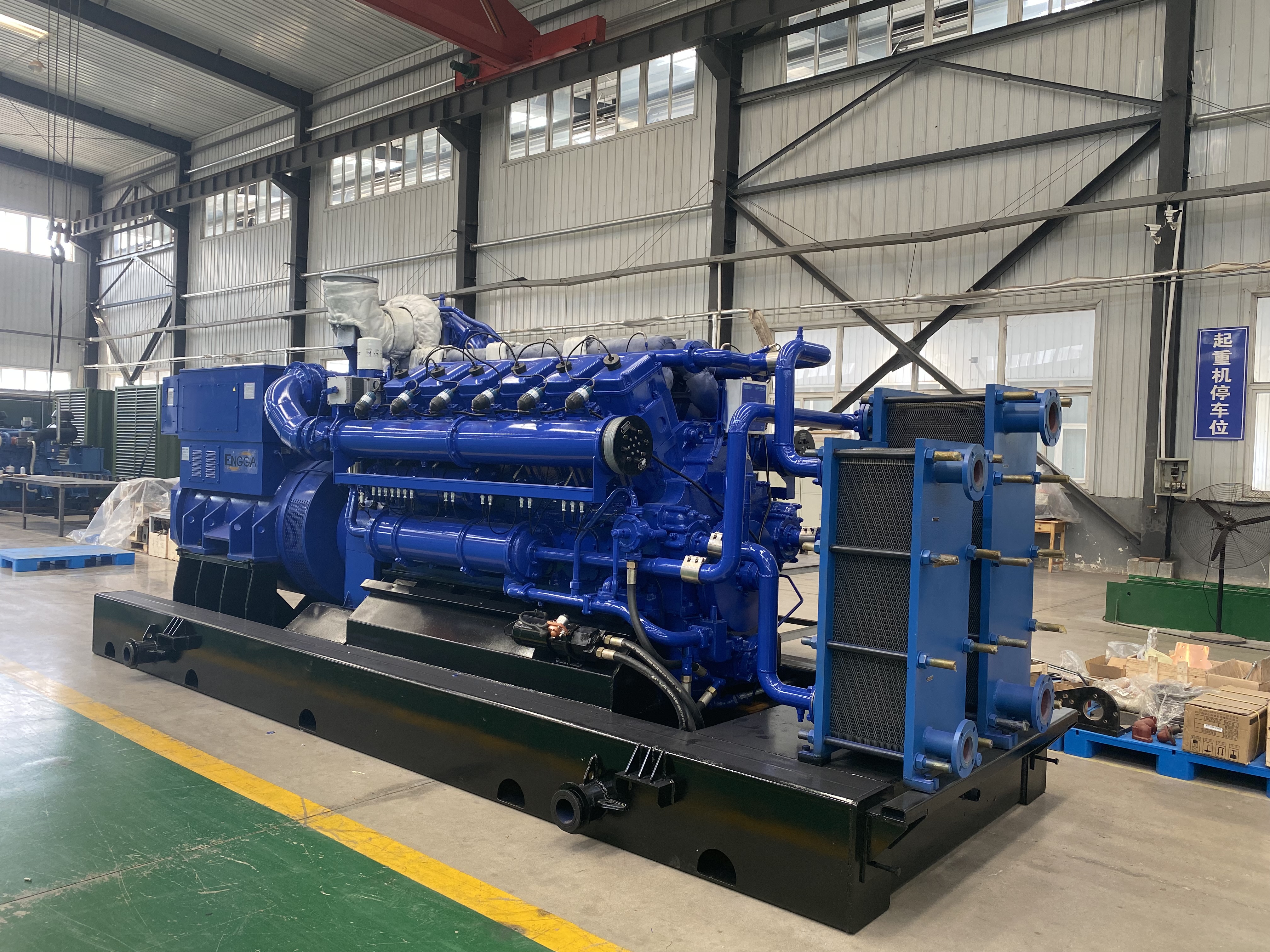
It is one of the key issues of repair quality to strictly ensure that the size of the fillet radius of the crankshaft journal of the natural gas generator set meets the drawing requirements. However, the general car repair shop does not pay enough attention to this. The grinding wheel is rarely polished, and the radius of the polished fillet is often smaller than the specified size. According to statistics, the fillet radius is less than 2.5 mm, and its fatigue strength is only less than 80% of that of 2.5 mm. Since the grinding wheel for smooth grinding of crankshaft is often trimmed with the grinding wheel fillet corrector attached to the grinding machine, so that the size of the grinding fillet meets the requirements, there has been no broken shaft since the vibration surfacing was put into production.
天然氣發(fā)電機(jī)組在工作中,曲軸由于受力和工作條件復(fù)雜,各摩擦表面滑動(dòng)速度很高,散熱條件又差,因此,曲軸的主軸頸和連桿軸頸在工作中不可避免地要產(chǎn)生磨損,而且磨損是不均勻的,其主要表現(xiàn)為軸頸出現(xiàn)圓度,圓柱度超過(guò)標(biāo)準(zhǔn)值和拉傷。連桿軸頸磨損的大部位,一般在各軸頸的內(nèi)側(cè)面上,即靠曲軸中心線一側(cè),使軸頸失圓;而磨損成錐形的部位,一般在潤(rùn)滑油道雜質(zhì)附著的一側(cè)和受力大的部位上。曲軸主軸頸_的磨損部位,按發(fā)動(dòng)機(jī)的強(qiáng)化程度、氣缸數(shù)、曲軸長(zhǎng)度和平衡塊的配重不同而各異,而且相對(duì)于連桿軸頸磨損要均勻些。實(shí)踐表明,連桿軸頸的磨損比主軸頸磨損要快,但是,主軸頸磨損比連桿軸頸磨損所造成的后果要嚴(yán)重。
During the operation of natural gas generator set, due to the complex stress and working conditions of the crankshaft, the sliding speed of each friction surface is very high, and the heat dissipation condition is poor. Therefore, the main journal and connecting rod journal of the crankshaft will inevitably wear during the operation, and the wear is uneven. The main performance is that the journal has roundness, cylindricity exceeds the standard value and strain. The most worn part of the connecting rod journal is generally on the inner side of each journal, that is, on the side of the crankshaft centerline, so that the journal is out of round; The parts that wear into a cone are generally on the side where the impurities in the lubricating oil channel attach and the parts with large stress. Crankshaft main journal_ The wear parts of the engine vary according to the degree of strengthening of the engine, the number of cylinders, the length of the crankshaft and the counterweight of the balance weight, and the wear is more uniform than that of the connecting rod journal. Practice shows that the wear of connecting rod journal is faster than that of main journal, but the wear of main journal is more serious than that of connecting rod journal.
天然氣發(fā)電機(jī)組檢驗(yàn)與處理方法。根據(jù)各軸頸磨損規(guī)律查找出磨損部位,可用外徑測(cè)微器測(cè)量其圓度和圓柱度以便確定曲軸的修理級(jí)別和磨削尺寸。
Inspection and treatment methods of natural gas generator set. Find out the worn part according to the wear rule of each journal, and measure its roundness and cylindricity with an outside micrometer to determine the repair level and grinding size of the crankshaft.
曲軸的光磨加工情況,是保證修復(fù)質(zhì)量的關(guān)鍵工序之一。以正時(shí)齒輪軸頸和飛輪突緣的外圓表面作為光磨裝-膏基準(zhǔn)時(shí),必須先校正彎曲度再進(jìn)行磨削,磨前中間主軸頸的擺差不得大于o.3毫米。如果不預(yù)先校正彎曲,織削以后將會(huì)使曲軸產(chǎn)生與原來(lái)飛輪突緣和正時(shí)齒輪軸線交叉的新軸線,改變了回轉(zhuǎn)半徑,破壞了動(dòng)平衡力,縮短使用壽命,加劇有關(guān)零件的磨耗,正時(shí)齒輪的響聲也大,后油封漏汕,增加了發(fā)動(dòng)機(jī)的不平衡旋轉(zhuǎn)質(zhì)量。
The smooth grinding of crankshaft is one of the key processes to ensure the repair quality. When the outer circle surface of the timing gear journal and the flywheel flange is used as the basis for smooth grinding, the curvature must be corrected before grinding, and the runout of the intermediate main journal before grinding shall not be greater than 0.3 mm. If the bending is not corrected in advance, after weaving, the crankshaft will produce a new axis that intersects with the original flywheel flange and the axis of the timing gear, which changes the turning radius, destroys the dynamic balance force, shortens the service life, and intensifies the wear of relevant parts. The noise of the timing gear is also loud, and the rear oil seal leaks, which increases the unbalanced rotating quality of the engine.
嚴(yán)格保證曲軸軸頸圓角半徑的尺寸符合圖紙要求,是修復(fù)質(zhì)量的關(guān)鍵性問(wèn)題之一。但一般汽車修理廠對(duì)此并沒(méi)有足夠的重視,砂輪很少修磨,光磨的圓角半徑常小于規(guī)定的尺寸。有資料統(tǒng)計(jì),圓角半徑小于2,5毫米,其疲勞強(qiáng)度只及圓角半徑為2.5毫米的80%以下。由于對(duì)光磨曲軸的砂輪,經(jīng)常用磨床附屬的砂輪圓角校正器修整,使磨得圓角尺寸符合要求,所以自振動(dòng)堆焊投產(chǎn)以來(lái),沒(méi)有發(fā)生過(guò)斷軸現(xiàn)象。
It is one of the key issues of repair quality to strictly ensure that the size of the crankshaft journal fillet radius meets the drawing requirements. However, the general car repair shop does not pay enough attention to this. The grinding wheel is rarely polished, and the radius of the polished fillet is often smaller than the specified size. According to statistics, the fillet radius is less than 2.5 mm, and its fatigue strength is only less than 80% of that of 2.5 mm. Since the grinding wheel for smooth grinding of crankshaft is often trimmed with the grinding wheel fillet corrector attached to the grinding machine, so that the size of the grinding fillet meets the requirements, there has been no broken shaft since the vibration surfacing was put into production.